Description
Previous
Next
Our scope of supply includes
- Heat-Exchanger Bundles with Welded Bonnet Headers, Removable Cover Plate- or Plug-Headers
- Horizontal, vertical, inclined arrangement (A-frame, V-frame)
- Axial fans in forced or induced draught installation
- Complete steel construction with ladders and walkways.
- Commissioning support & Site support
Our Services
- Thermal Design
- Mechanical Design
- Fabrication
- Re-tubing
- Commissioning Support
FEPL offers global solutions for thermal and mechanical design, detailed engineering to fabrication, testing and onsite assistance. We have shared thoughts and experience with all our customers to find the right exchanger for each particular situation, no matter how difficult it might seem.
Our mechanical engineering group performs efficiently in house large scientific and technical calculations, 2D-3D drafting works, Finite Elements Analysis.
Mechanical engineering, structural engineering is performed in accordance to international standards as API661/ASME VIII Div1. Earth quake (seismic) calculations and wind calculations are made following American standards/client selected code.
FEPLs factory is located in Ahmedabad, Gujarat. We fabricate new equipment as well we repair and recondition existing installations of finned tube aircooled heat exchangers for the chemical and Petrochemical industries.
The workshops are equipped with the most modern facilities for proper manufacturing and control such as:
Cutting machines
Various welding Equipments for manual and automatic processes (Arc-MIG- MAG-TIG-SAW-Weld-overlay).
Tube ends expanding machines
Finning machines (Extruded and Embedded, Wound-on)
Mobile cranes (capacity up to 30 tons)
Hydraulic plate rolls, Press Brake, Iron worker, Unfinning machine,
Drilling/milling
FEPL produces a wide range of ACHE equipment to 50 tonnes per unit. We work in a wide range of metals from carbon steel to high alloy steels. The selection of materials can be normal steel, stainless, CuNi, high quality material like inconel and duplex.
The FEPL production range covers all types of finned tubes with aluminium fins, steel fins, etc. The finning operations are completely carried out in our workshops and guaranteed by our periodic production tests. All tubes can be supplied with any kind of exchanger tube material and a wide choice of dimensions and thicknesses.
Priority during the manufacturing cycle to guarantee short delivery terms. Complete range of mechanical parts such as:
Aluminium or plastic fan blades
Fan hubs
“V”, HTD, etc. pulleys type and belts
Electric motors
Gearboxes
Other accessories
can be supplied within the shortest time. Among the most common spares needed for the air-cooled heat exchangers are plugs, gaskets and belts, subjects to frequent wear. Our well stocked warehouse put at your disposal, standard materials and dimensions, nearly upon immediate delivery. FEPL can supply replacements of pressure parts for air-cooled heat exchangers. All pressure parts are supplied in accordance with the same quality assurance as the original equipment and constructed following all pertinent international Codes and Regulations and certified, when required, by the main International Certification Bodies. Re-tubing of tube bundles can be made in our workshops. A special care in the workshop organization assures priority during the manufacturing cycle to guarantee short delivery terms.
Air Cooled Heat Exchanger Assembly
Air cooled heat exchangers are generally composed of the heat exchanger bundles for process cooling, the fans for the cooling air and the steel construction. Heating coils, louvers and maintenance platforms with access ladders are commonly used supplementary equipment.
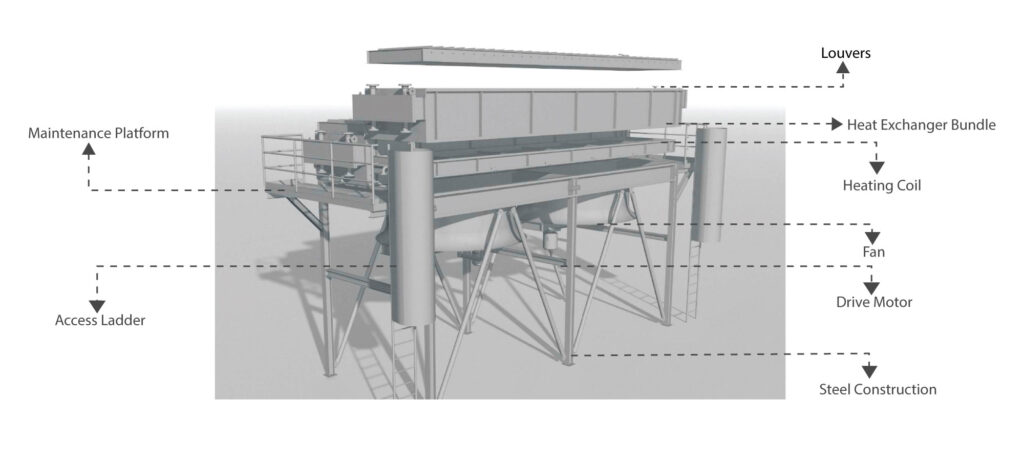
Configurations
With Forced Draught Fans
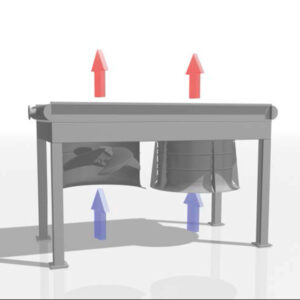
The horizontal arrangement of the heat exchanger bundles with forced draught fans underneath the bundles is the most common configuration of air cooled heat exchangers. It gives easy access to the fans and fan drives for maintenance purposes.
With Induced Draught Fans
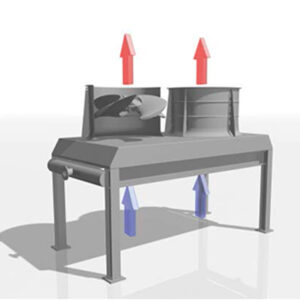
Induced draught arrangement of the fans above the heat exchanger bundles results in an even distribution of the cooling air to the heat exchanger surface. The plenum shades the heat exchanger surface and therefore protects it from solar radiation.
A-frame
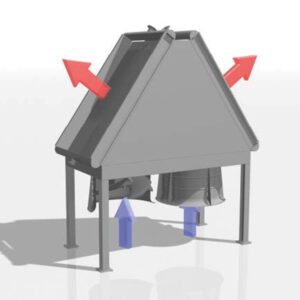
Air cooled heat exchangers in A-frame configuration are used when the plot area is restricted. The fans are arranged in forced draught.
Vertical Arrangement
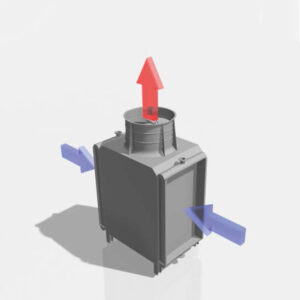
Air cooled heat exchangers with vertical arrangement of the heat exchanger bundles are used when the plot area is restricted. When the air flow through the fans is vertical they are installed with induced draught. Especially smaller coolers can also have fans with horizontal airflow (forced or induced).
Headers
Air cooled heat exchanger bundles can be equipped with different types of headers. Selection is based on the process requirements. Main criteria are the design pressure, cleaning requirements on the tube side and the requirement for access to the tube-to-tube sheet connection. Apart from the shown header types other solutions are also possible. For special applications FEPL can manufacture bundles with manifold headers, u-tubes or serpentine-coils.
Welded bonnet header
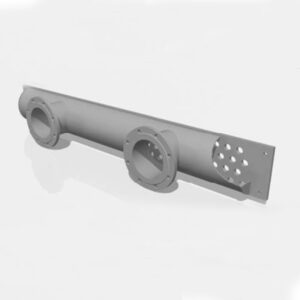
Here a bonnet header is welded to the tube sheet. The process nozzles are located on the bonnet. This header design is suitable for processes where no access the tubes or tube-to-tube sheet connection is required. The maximum design pressure is approximately 100 bar.
Removable cover plate
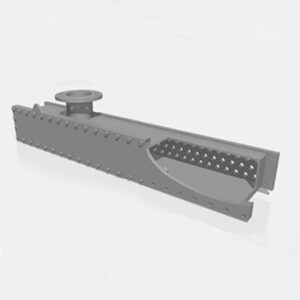
The header frame and the tube sheet form a box. The cover plate is mounted to the header box with a bolted flange connection. This design allows the removal of the cover plate for cleaning and maintenance purposes. The process nozzles can be located on the header frame or the cover plate. The maximum design pressure is approximately 50 bar. If higher design pressures are required special designs can be used.
Plug header
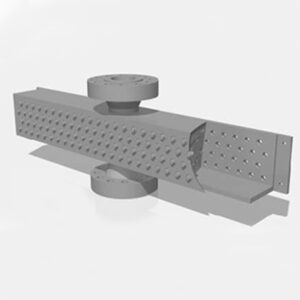
A plug header is a fully welded box header. Opposite of every heat exchanger tube a removable plug is installed in the plugsheet for cleaning and maintenance purposes. This header design can be used for high pressure applications up to approximately 250 bar.
Finned Tubes
B-Fin (extruded)
Previous
Next
Tubes with extruded aluminium fins have a high mechanical and thermal stability. The fin is extruded from an aluminium tube that is slid onto the core tube. That creates a strong bond between tube and fin with excellent heat conduction properties. Material fin: aluminium Material core tube: any metallic material. Max operating termperature: 300 °C
G-Fin (embedded)
Previous
Next
Tubes with embedded fins have very good heat conduction properties and a high thermal stability. The mechanical stability varies with the choice of fin material. The fin is spirally wound into a groove in the tube and tightly bonded to it by rolling. Material fin: aluminium, carbon steel Material core tube: carbon steel, stainless steel. Max operating termperature: 400 °C
L-Fin (wound on)
Previous
Next
Tubes with L-fins (or knurled L-fins) are used in environments with moderate requirements for the mechanical and thermal stability. During fabrication a fin-strip of aluminium is preformed into an L-shape and then wound onto the tube under tension. Material fin: aluminium Material core tube: any metallic material. Max operating termperature: 200 °C
I-Fin (wound on)
Previous
Next
This tube has a spirally wound, straight fin that is wrapped onto the tube under high tension. For corrosion protection of the fins either a galvanized fin-strip is used or the complete tubes are hot-dip galvanized after finning. Material fin: carbon steel Material core tube: any metallic material. Max operating termperature: 250-300 °C
Finned Tubes
Fans
The cooling air that is required for the cooling process is moved through the heat exchanger bundles by axial fans. The design of the fans and the selection of the fan type is based on the particular design point given by the heat exchanger design. Main criteria are the required volume flow of air, the pressure loss and the individual requirements regarding noise emissions.
General Assembly
The main components of an axial cooling fan are the fan ring, the fan impeller and the v-belt drive unit. Depending on the particular design requirements different blade profiles made of aluminium or glass fiber reinforced plastic (GRP) are used for the fan impellers. For the fan rings we are using a construction with an ellipsoid shape at the inlet side. This shape minimizes turbulence resulting in high energy efficiency and therefore reduced required power. Additionally noise emissions are optimized. The material for the fan rings is steel. For corrosion protection all parts are hot-dip galvanized. Alternatively painting or a combination of galvanizing and painting are possible
Drive Assembly
The main components of an axial cooling fan are the fan ring, the fan impeller and the v-belt drive unit. Depending on the particular design requirements different blade profiles made of aluminium or glass fiber reinforced plastic (GRP) are used for the fan impellers. For the fan rings we are using a construction with an ellipsoid shape at the inlet side. This shape minimizes turbulence resulting in high energy efficiency and therefore reduced required power. Additionally noise emissions are optimized. The material for the fan rings is steel. For corrosion protection all parts are hot-dip galvanized. Alternatively painting or a combination of galvanizing and painting are possible
Previous
Next
Spare Parts And Services
Our service is not limited to the main and most frequent replacements. We are available for any kind of supply according or not to our design; our experienced team can help you implementing and improving the performance of your equipment. A non-exhaustive list of the products, which can be supplied as complement of our units are:
- Vibration switches
- Vibration detectors
- Bearings
- Louvers
- Positioners
- Finned tubes
- Collars, tubes supports and any other parts as per your needs.
Previous
Next